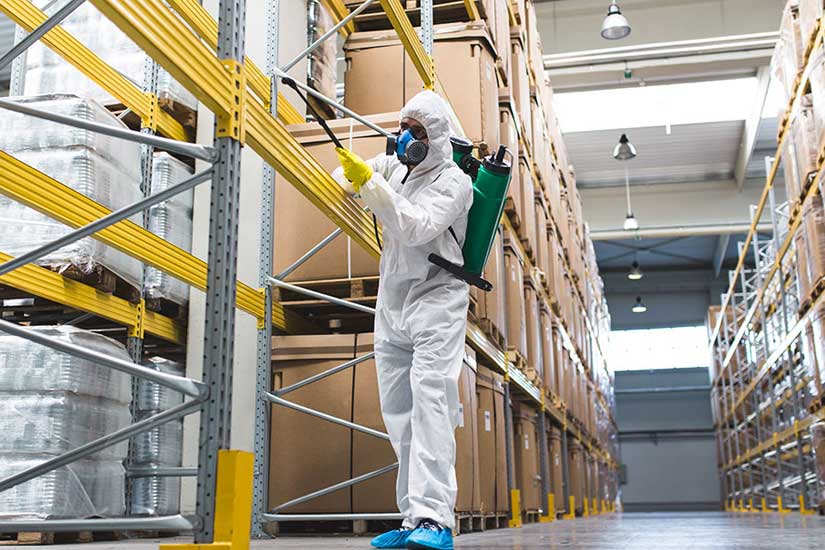
industrial hygiene
Keeping Workers Healthy and Safe
Industrial hygiene is concerned with identifying, evaluating, and controlling actual or potential workplace environmental stressors or hazards that can affect the well-being of workers and community members. Therefore, it is sometimes called Occupational Hygiene, Occupational Health, or Workplace Health. Ideally, hazards are identified and controlled when a workplace is being planned, conditions or processes change, or yearly reviews before they become an issue for workers.
To help ensure proper industrial hygiene and thus the health and safety of your workers, you can employ an industrial hygienist. The role of an industrial hygienist is to anticipate health and safety concerns and design solutions to prevent them. They are the guardians of workplace safety, applying science to identify and solve health and safety problems. Industrial hygienists also unite management, workers, and all segments of a company behind the common goal of health and safety. The American Board of Industrial Hygiene certifies industrial hygienists, providing a well-respected benchmark in the field.
An industrial hygienist will use rigorous scientific methods to evaluate and control hazards in the workplace, including risk assessment tools and information, such as Safety Data Sheets, which are put together by chemical manufacturers and contain detailed information about each chemical. Industrial hygienists can also conduct a worksite analysis to evaluate all jobs, operations, machinery, and work activities at that site, in addition to problem-solving on specific activities or work areas.
After a hazard is identified, an industrial hygienist will work with the company to control or eliminate the hazard. This can include substituting a chemical for a less hazardous one, reducing exposure to hazards, utilizing personal protective equipment such as gloves or goggles, or increasing ventilation.
- Ergonomics
- Noise
- Temperature
- Indoor air quality
- Chemical exposure
- Radiation
- Biological hazards
- Eliminating Hazards
- Controlling Hazards
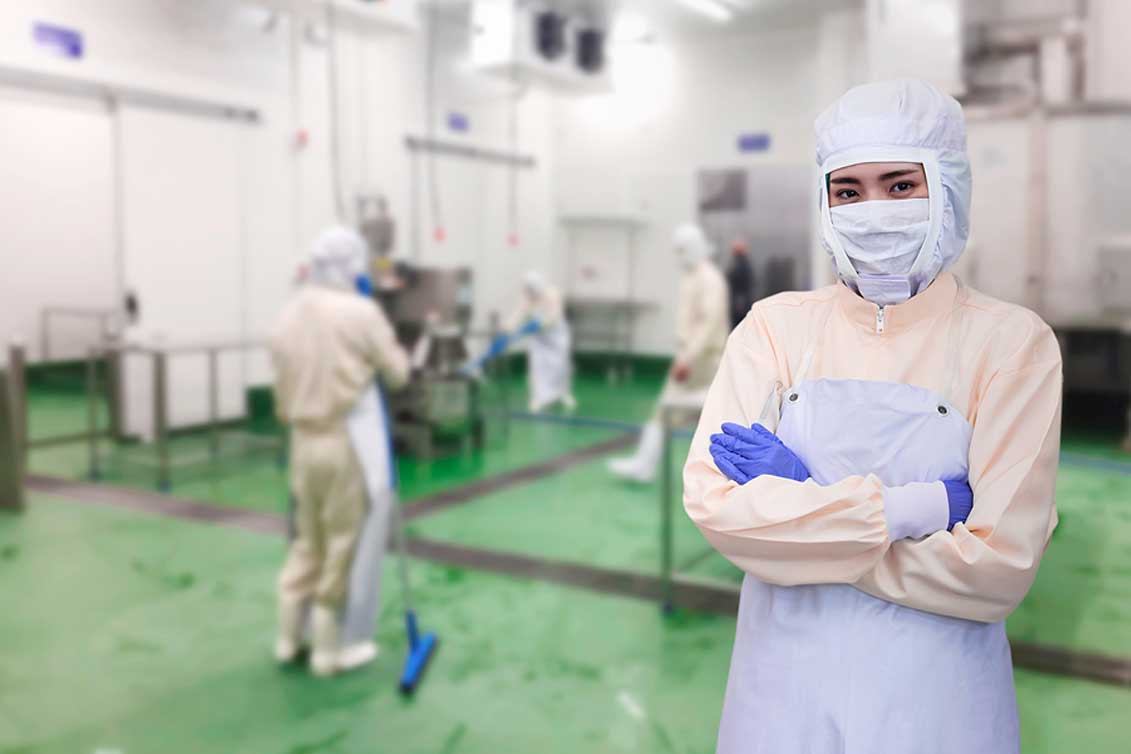
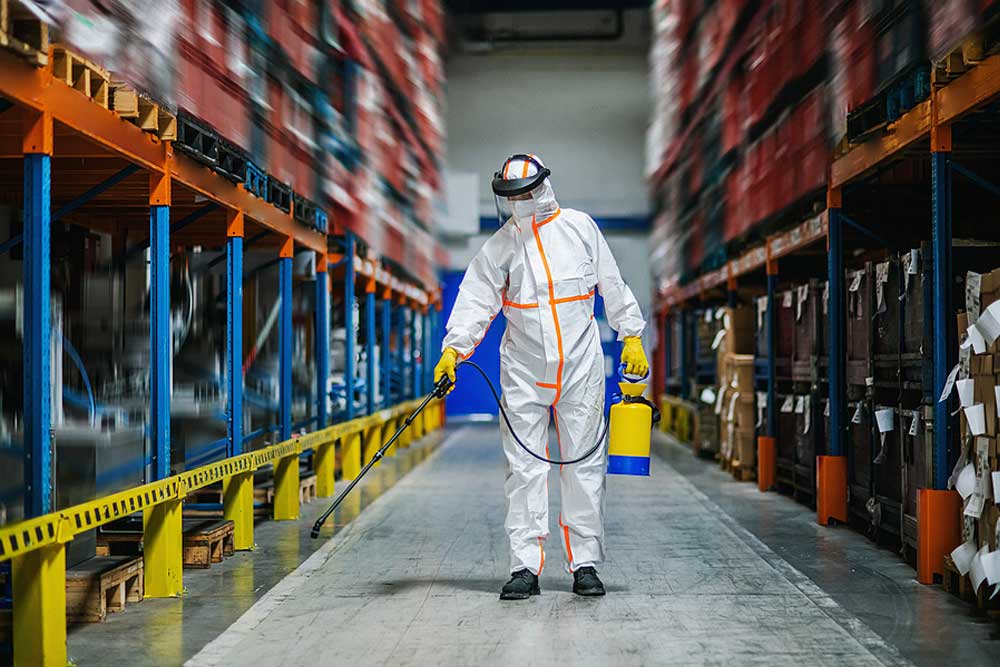