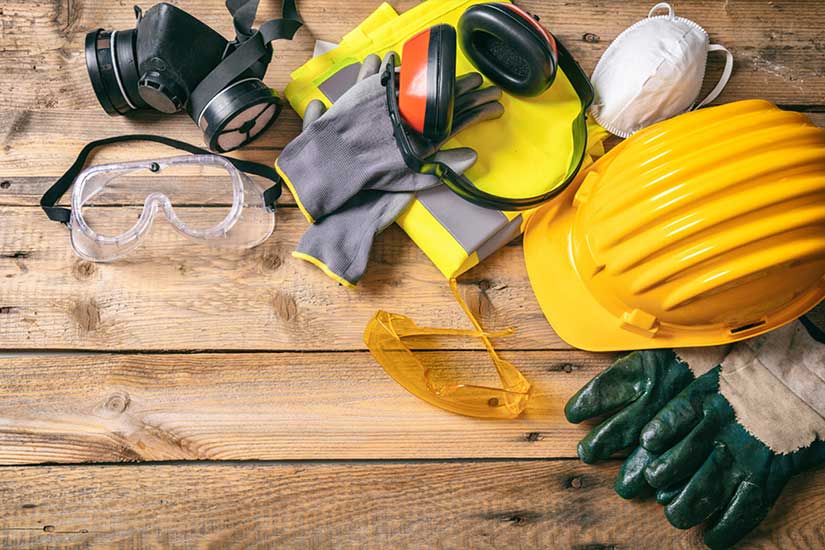
Safety Awareness
Awareness is safety
A safe workplace is an efficient workplace. When the proper safety protections are in place, workers feel safe doing their job, are more productive, and are more likely to take personal accountability and be engaged in work. Having a safe workplace is an ongoing process that involves a culture of safety, safety awareness, and safe practices and procedures. Safety awareness is a constant realization that every worker should have. It consists in being constantly aware of how they are working and recognizing the hazards they face. Safety awareness is essential in mitigating safety-related risks.
The safety of workers in the workplace should always be a priority. You need your workers to stay safe and perform their duties, so you have to ensure that the environment you put them in is safe enough for them to function. Ensuring worker safety means creating a safe, efficient, positive workplace where employees can focus on productivity. There are specific programs you must implement and focus on if you want to encourage an ideal safe environment for your workers.
A safe workplace is crucial, and ensuring that you have the proper safety procedures and policies for things such as working at heights, first aid CPR, confined space entry, and things like WHMIS can create a great work environment that is safe and productive. Since Courtice|Grasons founding, its diverse team of certified health and safety professionals has taken great pride in delivering prompt, cost-effective, and relevant workplace health and safety solutions.
The elements of the safety programs include the following:
- Communication and involvement between the employer and the employee in relation to safety and health issues in the workplace.
- A copy of the company’s employee safety and health policy.
- Encouragement of employee involvement in policy-making for health and safety issues.
- Participation in safety activities.
- Regular and timely analysis of workplace conditions in an effort to identify and eliminate potential or existing hazards.
- Ensuring the employees are aware of the hazard analysis for each job and process.
- Ensuring that workers are aware of how to operate and maintain their personal protective gear.
- Training workers to handle specific situations using the proper procedures.
- Only allowing people who are authorized and instructed to do certain jobs, to actually do them.
- Employees should be prepared with emergency drills.
- Ensuring that you focus on the employees that are learning new operations in the workplace, so that you know if they have all the necessary job skills and hazard awareness.
- Training managers and supervisor to spot hazards and understand what their responsibilities are in relation to them.
- Ergonomics
- Noise
- Temperature
- Indoor air quality
- Chemical exposure
- Radiation
- Biological hazards
- Eliminating Hazards
- Controlling Hazards
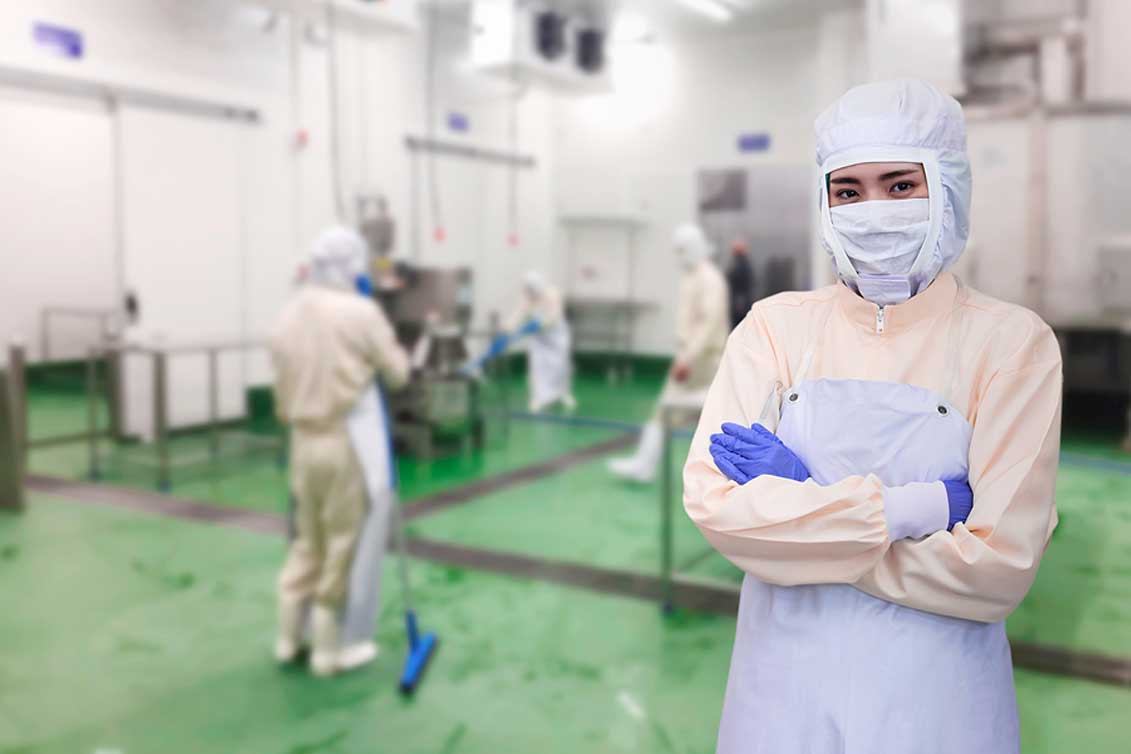
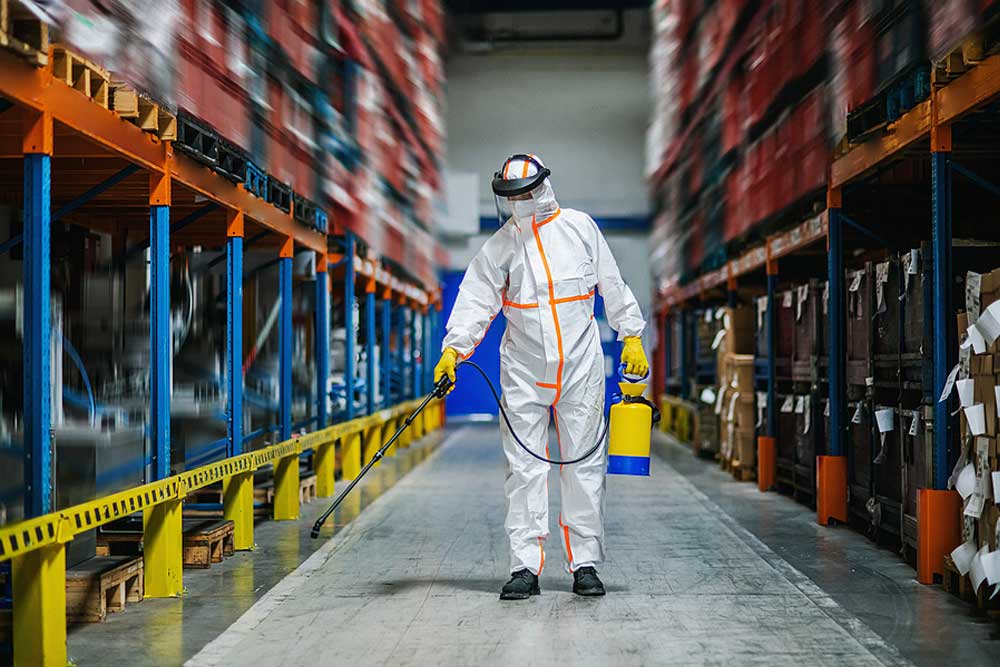